Our Applications
OUR MAIN
Applications

We at ProCone will consult our clients in the best way in how to use the produced SynGas to convert it to profitable, environmentally and socially acceptable products. With our wide range of processes we will find a solution that will fit all three main benchmarks’: economical, environmental and ethical projects only. This also involves other factors, for example, transportation logistics and pricing for the produced products, location of the off-takers, market accessibility, market forecast and much more. Keeping pace with technologies that evolve rapidly is critical to offer the client the best materials handling and management solution. Therefore, ProCone has assembled a team of experts that are well versed in the technology landscape. In addition, ProCone is working with other researchers and institutions engaging actively in new technologies, tools and methods.

Commercial Synthetic Gas Production
The SynGas produced can be utilized in different forms. The simplest form is to clean the SynGas to specification and to supply it into an existing gas network for heating or power generation purposes. This simple form of conversion requires only the materials treatment at the front end of the gasifier and a gas cleaner and gas compressor at the back end of the gasifier. This application can be found in regions where natural gas resources are limited but steam, electricity or heating requirements or a combination of it are in demand.
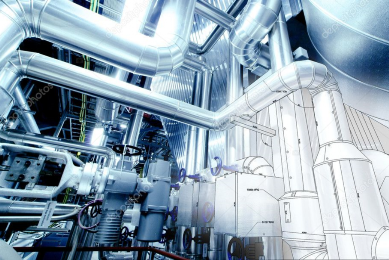
Power Plants with Gas Engines or
Integrated Gas Combined Cycle
The more commonly known application for SynGas is the production of electricity and heat at the site of gasification of the plant. ProCone distinguishes two different applications. Of the two applications the main end-product is electricity. However, excess heat produced by the power generator can be converted into steam or used for heat or cooling production mostly used in greenhouses. The two applications are as following: power plants with gas engines or power plants with gas turbines also known as Integrated Gas Combined Cycle (IGCC) plants.
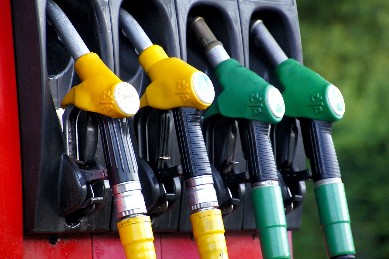
Bio- and Synthetic Fuels Production
ProCone's BASURAgas® Universal System converts different materials deriving from biomass, waste, and other sources into different fuels and liquids such as Bio-Diesel, Bio-Jet-Fuel, Bio-Ethanol, butanol, isobutene, isoprene or others on a low cost basis.
Synthetic fuels - SynFuel (diesel, gasoline, kerosene, ethanol, butanol, etc.) essentially have a significant advantage over fossil fuels. Since SynFuel is produced purely synthetically, the product has a high, almost perfect degree of purity.

Paraffin Wax Production
ProCone's BASURAgas® Universal System converts different materials deriving from biomass, waste, coal and other sources into pure paraffin wax on a low cost basis. This form of conversion requires the materials treatment at the front end of the gasifier and a gas cleaner, gas compressor and Fischer-Tropsch conversion unit at the back end of the gasifier as the basic configuration. This application can be found anywhere were paraffin wax is in demand or suitable feedstock materials are available.

Carbon Black Production
Carbon Black is a by-product when methane plasmolysis as the core process is used to produce hydrogen. To convert the produced SynGas from the ProCone's BASURAgas® Universal System into carbon black and hydrogen, the required processes after the CO2 capturing, in combination with electricity and steam produced by ProCone’s integrated power plant are the electrolysers, the methanation and methane plasmolysis. Carbon Black yields a high value in the market for construction, battery manufacturing, light weight construction, paints, tires, agriculture and many more.
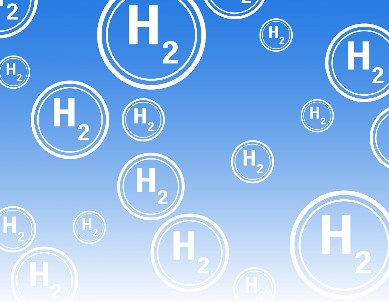
Hydrogen Production
Trough methane plasmolysis ProCone produces hydrogen with a purity of 99.9%. ProCone strives to produce blue and green hydrogen using 75% less energy than the technology mainly used today namely the Steam Methane Reforming (SMR) process. Hydrogen received a wide recognition as a clean energy supplier without any CO2 release. In today's environmentally conscious social environment, hydrogen as an energy source especially in the transport industry is becoming important.

Wastewater Treatment Sludge
ProCone's BASURAgas® Universal System converts WWT sludge deriving from industrial or municipal WWT into electricity, heat, steam, biofuels or other chemical materials on a low cost basis. In addition, vital phosphorus in a highly purified form is provided for agricultural use along with other important fertilizers such as potassium, magnesium, sulfur and nitrogen.
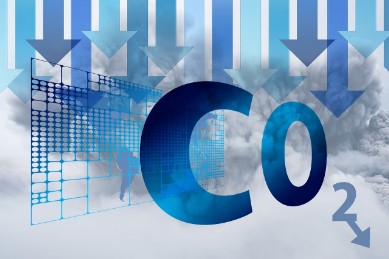
Carbon Capture and Sequestration
ProCone’s carbon capture and sequestration components ensure a high efficiency and low operational cost. This technology is used in the Hydrogen production, but also can be implemented to produce synthetic liquids. The main goal should always be the reduction of the CO2 output to the environment or even to be carbon neutral. CO2 can be commercially marketed and placed to productive use.

Coal Conversion
The BASURAgas® universal plant for converting coal into profitable chemicals and fuels consists of five main processes: the coal preparation unit, the thermochemical conversion, the SynGas cleaning and upgrading and a) the biochemical conversion or b) the Fischer–Tropsch synthesis. The fifth process uses the purge gases and a portion of the original SynGas to generate electricity and steam to power the entire plant.
OUR
Facilities

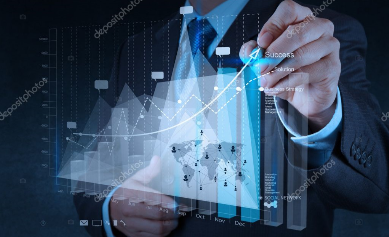
Plant Configuration
ProCone offers the BASURAgas® Universal System in different configurations. See below some of the configurations possible. A combination of feedstock materials is also possible. In addition, the product produced can be different from one production line to the other in the same plant. Please contact ProCone if you do not see your feedstock material or for any other configuration question.

Plant Size
ProCone offers different sizes of plant configuration. The most important factors are feedstock materials on a continuous basis, capital investment, and plant land availability. However, the size of the facility can also depend on the market demand of the end product. It is also possible to operate several production lines. All of these variations will be evaluated in the feasibility study.